3D打印鞋履:未来制鞋业的必争赛道!
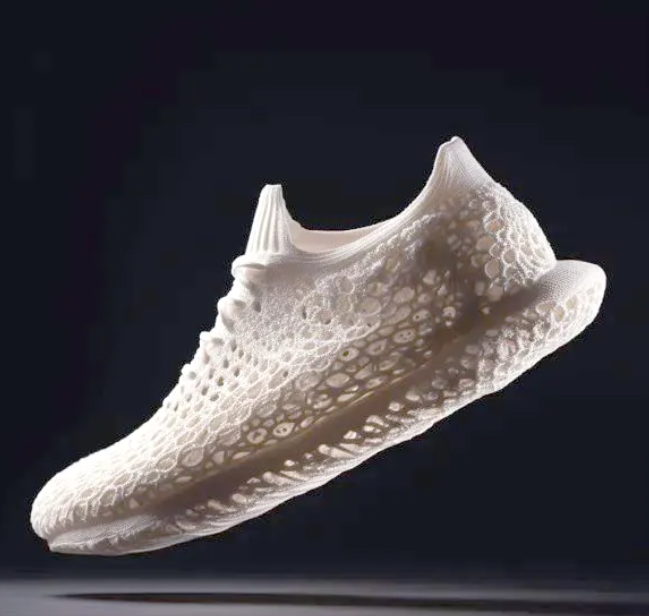
(图片来源网络侵删)
当一双双无需针线缝合、由打印机层层“生长”的鞋子从实验室走向市场,3D 打印正改写制鞋产业的规则。当前,3D打印在鞋领域的应用已经从概念产品到限量发售,再到部分品类量产,已经“进化”至“如何规模化”的攻坚阶段。
这场鞋业变革,不仅预示着鞋类从标准化生产向个性化定制的深层变革,甚至可能重塑全球鞋业竞争格局,一些率先掌握核心技术与产业化能力的企业,将在柔性生产时代占据先机。
01
鞋品牌3D 打印实践:从定制探索到量产突破
.png)
(图片来源网络侵删)
日前,耐克与Zellerfedld携手打造的3D打印运动鞋Air Max 1000推出蓝色新版本,仅在法国巴黎出售。这是耐克基于去年11月首次发布Air Max 1000 3D打印运动鞋之后的市场表现,在3D打印鞋领域的又一次尝试。
耐克Air Max 1000 3D鞋去年推出市场后虽然未公布具体销量,但二级市场价格一度飙升至原价210美元的3-5倍,显示市场对该技术的强烈兴趣。
耐克早期就曾探索3D打印在运动鞋中的应用潜力,但未大规模量产。在2017年推出的一款产品中,耐克就是采用3D打印纺织鞋面(Flyprint技术),而非传统编织工艺。目前,耐克已然将3D打印技术应用作为其创新战略的支柱。
事实上,3D打印技术在鞋类制造领域的应用已从概念验证逐步走向商业化,众多国际运动品牌和国内厂商纷纷推出创新产品。
.png)
(图片来源网络侵删)
例如,阿迪达斯的4DFWD系列采用Carbon公司的光固化3D打印技术,中底采用弹性晶格结构,可根据不同运动需求调整缓震性能。2023年通过优化晶格结构,提升能量回弹效率,年产量超10万双。
新百伦推出的一款专业跑鞋采用SLS(选择性激光烧结)3D打印技术,鞋底采用蜂窝结构,提供动态支撑。
亚瑟士曾与清锋科技合作,推出3D打印鞋限量发售款。采用光固化3D打印弹性体材料,鞋底采用参数化晶格结构,优化软硬度和透气性。
而国货品牌匹克近日发售的3D打印“遨游”拖鞋,更是成为面向大众消费的量产化3D打印鞋款,采用博理科技HALS超高速光固化打印,鞋身一体成型制造,无需传统拼接工艺,目前已经在多个购物平台上同步发售。
根据市场研究机构Vantage Market Research 关于3D打印鞋市场预测的报告显示,预测2030年市场规模达36.6亿美元。但从目前的行业数据来看,当前3D打印鞋成功案例仍然仅仅集中于高端定制与小批量生产,印证3D打印鞋技术仍处从概念到商品的过渡期。
02
3D打印企业的渗透:多元合作与生态构建
3D打印企业在鞋类制造领域的渗透,已从单纯的设备供应转向全产业链深度介入,通过技术绑定、工艺重构与生态共建,形成了多元合作模式与梯度化产业布局。
在金属3D打印领域,联泰科技、铂力特等企业专注于鞋模制造的革新。其中联泰科技金属3D打印中心,宣称可将传统7天的模具开发周期缩短至14小时。
新兴力量恒锐科技凭借其原有领域的光学技术优势,在金属3D打印设备领域表现突出,其自主研发的环形可变光斑技术,为鞋模制造提供了高效解决方案。
.png)
(图片来源网络侵删)
在光固化技术路线中,博理科技与匹克的合作颇具代表性。其开发的双组分树脂材料和超高速打印技术,在匹克“遨游”3D打印拖鞋等产品中得到应用,实现了鞋款一体成型与量产落地。
而金石三维目前已形成覆盖“设备+材料+软件+服务”全链条的 3D 打印产业体系,鞋业服务涵盖木模替代、金属模具、成品鞋打印等板块,形成了从设计软件到终端产品的全价值链服务模式。在产业布局上,已建立越南最大的数字化应用中心,并参与温州鞋企的设备升级改造,以“解决方案”模式成为行业标杆。
在材料领域,中体新材、众远新材、北矿新材等厂商提供的铁基合金、钛合金等金属粉末,以及适配光固化工艺的弹性体树脂,为 3D 打印鞋的量产提供了基础材料支撑。
国外企业中,Carbon与阿迪达斯的合作是光固化技术在鞋类制造中商业化应用的典型案例。双方合作的4DFWD 系列2023年产量突破10万双,这一规模反映出光固化技术在量产层面的实际进展。
而Zellerfeld与耐克合作的 Air Max 1000,作为一款几乎完全由 3D 打印制造的一体式运动鞋,展现了 FDM 技术在鞋款一体化成型上的探索,但该技术路线在日常穿着的耐用性与舒适度方面,仍需行业进一步验证。
.png)
(图片来源网络侵删)
从产业布局来看,国内 3D 打印企业已形成“技术研发-区域落地-全球拓展”的梯度。比如金石三维在珠海、平湖等地建立六大产业基地,覆盖华南、华东等鞋企集中区;博理科技以上海为中心,辐射长三角品牌集群;联泰科技则深耕晋江、莆田等传统制鞋产业带。这种布局既贴近鞋企生产需求,又能快速响应供应链调整,为技术迭代与商业化落地提供了地理支撑。
03
3D 打印的瓶颈突破与未来图景
.png)
(图片来源网络侵删)
3D打印技术在鞋类制造领域,正处于从技术探索向规模化应用过渡的阶段。
技术层面,3D打印不同工艺的适用性仍需打磨。FDM 技术一体化设计优势显著,但材料长期耐磨损性与脚感稳定性需更多市场验证;光固化技术虽实现量产,却在材料成本控制、打印精度与纹理一致性上仍有提升空间,以适配更复杂的鞋款需求。
生产效率上,3D打印的单件生产特性与传统流水线的批量产出能力存在差距。金属 3D 打印鞋模虽能缩短开发周期,但其成本优势仅限复杂花纹或小批量场景,大规模应用需平衡经济性与效率。
材料体系方面,适配3D打印的鞋用材料虽在弹性、透气性等指标上接近传统材料,但品类有限,难以覆盖全品类鞋款,且长期使用性能数据积累不足。
虽然当前仍面临一些发展上的挑战,但也孕育着突破的新机遇。面对这些难点,行业正从多维度探索突破。
.png)
(图片来源网络侵删)
技术上,聚焦材料改良与设备升级:研发更耐老化、低成本的弹性体树脂与轻量化金属材料,拓宽材料品类;优化设备光学系统与扫描路径,提升打印效率与精度。
生产模式上,推动“集群化+智能化”转型,通过设备集群管理与智能调度提升单位产出,推动后处理自动化以降本,缩小与传统流水线的效率差距。
产业生态上,强化协同与标准共建:鞋企与3D打印企业联合制定材料标准与设备规范,推动设计工具与打印工艺融合以减少损耗;同时通过“技术落地+体验升级” 培育市场认知,让消费者从“感知新奇”转向“认同价值”。
.png)
(图片来源网络侵删)
展望未来,3D 打印在鞋领域的前景清晰可及。短期内,将在中底、定制拖鞋等场景实现更大规模量产,成为品牌差异化竞争的关键。长期来看,3D 打印将重构鞋业制造模式,实现“个性化定制+快速生产”:消费者在线定制鞋款,企业快速响应以减少库存,同时与传统工艺形成“个性化+规模化”的混合体系,推动行业向更高效、灵活、贴合需求的方向升级。